CASE STUDY
How a Leading British Pharma Company Leveraged the Veratrak Hub Platform
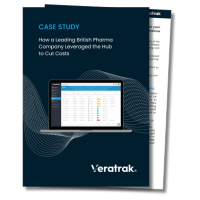
Read our case study to discover how a British pharmaceutical company reduced their operational integration costs and streamlined activities with their logistics services providers by leveraging Veratrak’s Hub platform.
Customer Profile
- Top 10 Global Pharma (UK based)
- £100 million per year spent on outsourcing consultants to manage partners’ interfaces
Background
A leading British Pharma company faced substantial costs and operational challenges related to managing global interfaces with third-party logistics providers (3PLs).
With expenditures exceeding £100 million annually on outsourced consultants for interface maintenance and support, they sought a more efficient and proactive solution to mitigate risks and reduce dependency on external support.
Veratrak’s engagement identified a 58% opportunity to reduce effort once warehouses are connected to the Hub platform, and a 40% cost reduction opportunity.
The Challenge
Despite the significant investment in outsourcing, the Pharma company encountered critical issues with operational interfaces that had severe impacts when they occurred. Often, notifications of these issues from 3PLs were delayed, reaching the company’s consultants only 24 hours after the problem had already occurred.
This delay hindered swift resolution and necessitated exhaustive efforts to identify and rectify the root cause, resulting in prolonged downtime and operational inefficiencies.
The Solution
Veratrak collaborated closely with the Pharma company to map their current processes, identify key stakeholders for integration development, support, and 3PL data consumption to deliver the following:
Real-time Error Monitoring:
Veratrak’s solution continuously monitored operational interfaces with 3PLs in real-time, identifying issues such as connection failures, mapping errors, translation discrepancies, and business logic inconsistencies.
Categorisation and Escalation:
Each identified issue was categorised based on its severity and impact, ensuring immediate escalation to the appropriate team or individual within the Pharma company. This proactive approach replaced the reactive crisis management previously necessitated by delayed notifications.
Proactive Alerting:
Alerts were generated instantly upon detection of any interface issue, enabling swift response and resolution. This proactive alerting mechanism significantly reduced downtime and minimised the operational disruption caused by interface failures.
The Outcome
The implementation of Veratrak’s proactive error monitoring and alerting system delivered substantial benefits to the Pharma company, as follows:
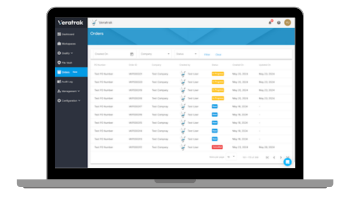
☑️ Reduced Activities across Supply Chain & Provider Ecosystem:
By empowering internal teams with real-time insights and proactive alerts, the Pharma company reduced their reliance on costly outsourced consultants for interface troubleshooting and maintenance.
Leveraging client knowledge of the integration processes, future Hub integration efforts were reduced from 414 days of effort to an average of 175 days, and timelines from 6-9 months to ~3 months.
☑️ Improved Error Visibility:
Enhanced visibility into critical operational flows with 3PLs allowed for preemptive action, preventing potential disruptions before they impacted operations.
☑️ Cost Savings and Efficiency:
The combination of reduced consultancy dependency and improved error management translated into significant cost savings and operational efficiencies for the Pharma company.
To move from the current point-to-point warehouse integration model to an integrated warehouse platform, Veratrak identified equivalent cost savings of over £500k per annum and £2.7m over five years.
Discover the Supply Chain Integration Modules Available in The Hub
Pharmaceutical Supply Chain Management
News, Events & Insights
Latest Industry Insights From LogiPharma 2025
Faced with regulatory requirements, geopolitical developments, sustainability pressures and operational complexity, supply chain leaders can no longer...
Mastering External Manufacturing Collaboration
Optimising external manufacturing cost-effectiveness while maintaining high-quality standards and regulatory compliance is increasingly complex and ch...
How a British pharma company reduced their systems integration costs
Read this case study to discover how a British pharmaceutical manufacturer reduced their operational integration costs and streamlined activities with...
MFA: The Key to Enhanced Digital Security
Relying on a password alone is not enough to keep online accounts safe; many sectors, particularly in life sciences and finance, require stringent sec...
Get in touch!
Interested in working together to optimise your supply chain sustainability? We'd love to hear from you.